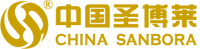
Products Introduction
The medium used for the high-temperature anti-cokingwear-resistant ball valve in the coking unit is generally oil containing cokepowder, vacuum residue and steam, and the working temperature is about 500 °C.Under this working condition, the valve must have the functions of corrosionresistance, wear resistance, erosion resistance, anti-coking and quick cuttingunder the conditions of easy coking and high temperature for a long time. Thebellows anti-coking ball valve is provided with a bellows behind the valveseat. Due to the elastic loading structure of the bellows, it can ensure theclose contact between the ball sealing surface and the sealing surface of thevalve seat under normal closing conditions, and can effectively compensate athigh temperature. The inner part is thermally expanded to avoid the jammingcaused by high temperature, which effectively solves the harmful effects of thevalve in the coking device against high temperature, coking, and erosionresistance. Its unique hard sealing surface has self-grinding effect, whichmakes it improve the sealing performance during the application of wear anderosion materials. It can work continuously under long-term conditions undersevere working conditions, and its service life is several times longer thanother valves.
Production Design Specification
Design&Manufacture:ASME B16.34、API 608、GB/T 12237
End to End :ASME B16.10、GB/T 12221
Connection :ASME/ANSI B16.5;ASME B16.25;HG20615;GB;JB;JIS;BS;DIN
Inspection & Test :ASME B16.104;API 598;GB/T 26480;ISO 5208
Product Features
Full-bore:The diameter of the sphere passage is the same as the diameter of the pipeline,the flow resistance is small, the circulation capacity is large, and the slagdischarge is convenient.
Splitball valve: The valve seat at the inlet end of the anti-coking ball valve is abellows valve seat, the outlet end is a metal valve seat that can slide in thevalve body embedding groove, and a gasket is arranged between the valve bodyand the valve seat.
Adoptingthe structure of the scraping valve seat: In order to prevent the coke powderparticles from entering the valve seat, the sealing surface of the valve seatis designed with a scraping structure with a sharp edge.
For the coke powder flushing condition,the spherical and valve seat sealing surfaces adopt supersonic sprayingtechnology, and the sealing surface hardness is improved by spraying differentmaterials to improve the service life of erosion resistance and wearresistance.
Bellows seat seal design: In order to ensurethe actual running time (with medium pressure), there is an initial contactpressure between the seat and the ball. The inlet end seat is made of a unique design of thebellows. When the temperature and pressure are alternating, Always give theseat a thrust so that it rests tightly against the ball. Under the combined action of the mediumpressure, the seat is leaked to ANSI/ FCI Class V. At the same time, in orderto prevent over pressure in the middle cavity,the valve seat compresses thebellows under the action of the pressure of the middle cavity, andautomatically discharges the pressure into the passage to ensure safe andreliable operation of the valve. The bellows adopts Inconel 625 super alloymaterial to ensure the contact betweenthe sealing surface of the ball and the sealing surface of the valve seat undernormal closing conditions. It can effectively compensate the thermal expansionof the inner part under high temperature and avoid the jamming caused by hightemperature.
Bellows steam purge design:This design caneffectively prevent the medium from entering the bellows and cause the bellowsto lose elasticity due to coking, and also prevent the valve leakage caused bythe uneven pressing force of the valve seat due to vibration during thedecoking process.
Valve chamber and stuffing box steam purgingdesign: purging the valve chamber and stuffing box can prevent the coke fromcoking or depositing, effectively solving the problem that the valve inner partcan not be opened due to the residue of the residue, and is effective protect the packing at the same time.
Live load packing design: the butterflyspring pre-tightening (ie live-load structure) is set between the packingcompression stud and the packing compression nut. The high-temperatureanti-coking ball valve can change the pre-tightening force of the combinedpacking in the temperature and stress alternating Continuity compensation isobtained to reduce the possibility of the packing leaking from the valve stemdue to the sudden loss of pressure due to the preload.
Selection of actuators:The selection of hightemperature anti-coking ball valve actuators has been considered. Over time,the expansion or contraction of the pipeline during coking or deposition ortemperature exchange requires the actuator to have a large torque and determinethe safety factor of more than 2 times.
Combination Of Material
Shell | Ball | Seat Ring | Stem |
A217 C12 F11/F22/F5 F304H/F316H/F321 | A182 F9+STL/N/WC/Ni F11/F22/F5+STL/N/WC/Ni F304H/F316H/F321+STL/N/WC/Ni | A182 F9+STL/N/WC/Ni F11/F22/F5+STL/N/WC/Ni F304H/F316H/F321+STL/N/WC/Ni | A638 660+STL/N/WC/Ni INCONEL X-718 F304H/F316H/F321+QPQ |
Product Range
Nominal Size:1/2”-16”
Pressure Rating:150LB-600LB(PN16~100Mpa)
SuitableTemperature:-29~538℃
Applicable medium: catalyst, slagreduction, circulating oil and gas mixture, containing coke powder
Operation:Hand wheel ,Gear box, Electric ,Pneumatic